Filter Cartridges
Filter elements suited to the most recent condensate filtering requirements in both conventional and nuclear power plants
This new range of filter elements embodies thirty years of technological progress and constant research by our company into every aspect of condensate filtration. The new frontiers opened up by the introduction of oxidizing chemistry - in many power plants has raised the question of how to enable existing condensate treatment filters to trap the more penetrating iron oxides produced by modified chemical/physical conditions. Consequently, we decided to follow the application of a new range of filter elements aimed to satisfy these sophisticated operating conditions.
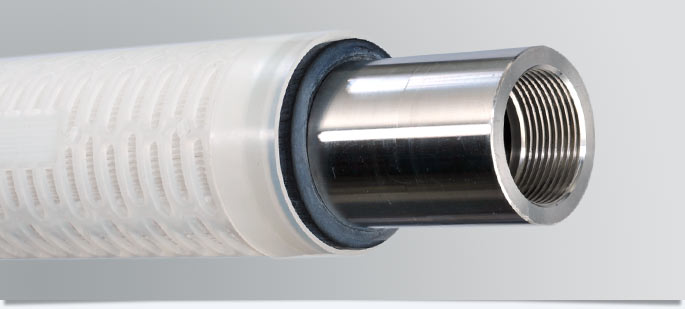
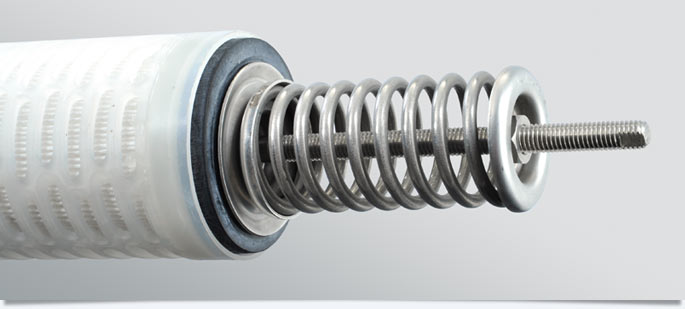
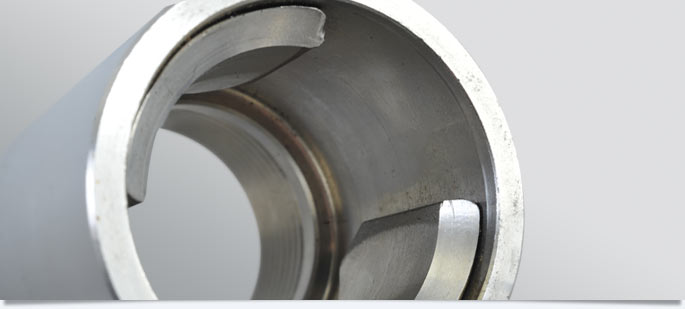
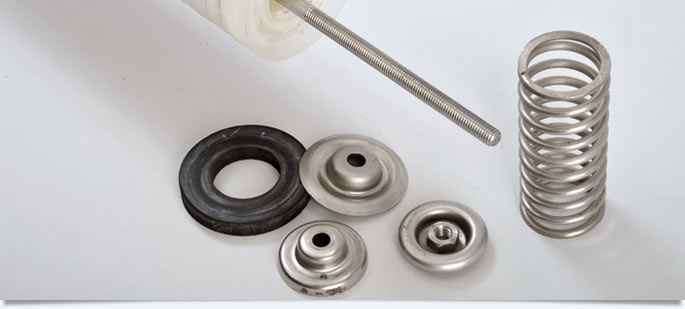
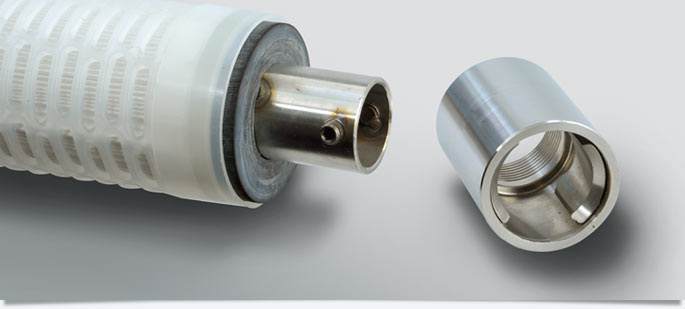
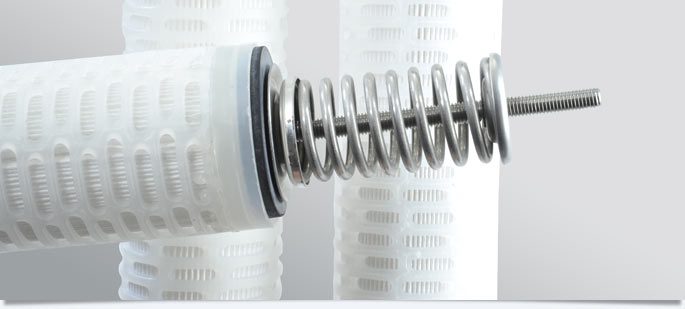
These elements can be roughly divided into four types:
A) Polypropylene wound elements
B) Polypropylene wound elements with reduced filtering thickness
C) Coatable pleated elements
D) Pleated elements
A) POLYPROPYLENE WOUND ELEMENTS
The filter element consists of a strong plastic or stainless steel core onto which a purified polypropylene thread is wound according to a pattern designed to induce optimum coating with medium-to-fine floc size powdered resins or inert materials (alpha cellulose, PAN, Pes). The type of thread used combines to limit oxide accumulation between the threads, thus increasing the filter element’s life.
Supports for filter element installation within main filters can be supplied upon request. These supports consist of strong stainless steel support complete with a spring-loaded compensating system and bayonet-type hook-in mechanism at the bottom. In addition, they have a head seal and can be adapted for use in all plant types.
Outer diameter: | 50/65 mm |
Sizes (lengths) available: | 60/70/80” |
Porosity: | 3-5-10 nominal microns |
Recommended backwashing: | air and water |
Max recommended running Δp: | 0,8 bar useing inert fibers as precoat and 1,5 bar useing powdered resins |
stainless steel support complete with a spring-loaded compensating system and bayonet-type hook-in mechanism at the bottom, and have a head seal. They can be adapted for use in all plant types.
Fields of Application
The above-mentioned filter element is suitable for those systems requiring use of powdered resins and/or inert filter products as coating materials, in other words all condensate treatment circuits with pre-filter units.
B) POLYPROPYLENE WOUND ELEMENTS WITH REDUCED WOUND FILTERING THICKNESS
The filter element consists of a strong plastic or stainless steel core onto which a purified antioxidant added polypropylene thread is wound according to a pattern designed to induce optimum coating with medium-to-fine floc size powdered resins or inert materials (alpha cellulose, PAN, PES). The type of thread used and its thickness combine to limit oxide accumulation between the threads, thus increasing the filter element’s life under high flow rate.
Supports for filter element installation within main filters can be supplied upon request.
Outer diameter: | 65 mm |
Sizes (lengths) available: | 60/70/80” |
Porosity: | 3-5-10 nominal microns |
Recommended backwashing: | air and water |
Max Recommended running Δp: | 0,8 bar useing inert fibers as precoat and 1,5 bar useing powdered resins |
These supports consist of strong stainless steel support with a loaded compensating system and bayonet-type hook-in mechanism at the bottom. They also, have a head seal and can be. adapted for use in all plant types.
Fields of Application
The above-mentioned filter element is suitable fored systems requiring use of powdered resins and/or inert filter products as coating materials, in other words all condensate treatment circuits with pre-filter units.
C) COATABLE PLEATED ELEMENTS
These filter elements consist of a strong polypropylene or stainless steel core onto which a polypropylene membrane is pleated. The pleated membrane is enclosed within a polypropylene support membrane. A suitably-sized external polypropylene cage improves the element’s strength.
The filter element is designed to achieve two goals: maximum-efficiency external element coating and capture of any iron oxide particle leakage which slipped past the material’s filtering action. This combined result provides extremely positive running advantages.
Filter media | polypropylene, polyester |
Available size (O.D.) | 63/65 mm |
Lengths: | 60/70/80” |
Porosity: | 1-3-5-10 microns nominal or absolute |
Recommended backwashing: | air and water |
Max Recommended running Δp: | 0.35 bar over initial Δp |
Supports for filter element installation within main filters can be supplied upon request. These supports consist of strong stainless steel support complete with a spring-loaded compensating system and bayonet-type hook-in mechanism at the bottom. They also have a head seal and can be adapted for use in all plant types.
Fields of Application
The filter element described above is suitable for systems requiring use of powdered resins and/or inert filter products as coating materials, hence all condensate treatment circuits with pre-filter units.
D) PLEATED ELEMENTS
This filter element consists of a strong polypropylene or stainless steel core onto which a polypropylene membrane is pleated. The pleated membrane is enclosed within a polypropylene outer support membrane. This type of filter element cannot be coated with filter materials.
Supports for filter element installation within main filters can be supplied on request. These supports consist of strong stainless steel support complete with a spring-loaded compensating system and bayonet-type hook-in mechanism at the bottom. They also have a head seal and can be adapted for use in all plant types. bottom, and have a head seal.
Filter media | polypropylene, polyester |
Sizes available (O.D.) | 63/65 mm |
Lengths: | 60/70/80” |
Porosity: | 1-3-5-10 microns nominal or absolute |
Recommended backwashing: | air and water |
Max running Δp: | 0.35 bar over initial Δp |
Fields of Application
The above-mentioned filter element is suitable for those systems which do NOT require use of powdered resins and/or inert filter products as coating materials, therefore all condensate treatment circuits with low-pressure generators or, alternatively, all plants including mixed resin beds.